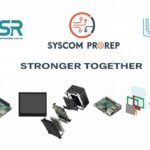
6 étapes pour planifier et éviter avec succès les coûts de l’obsolescence
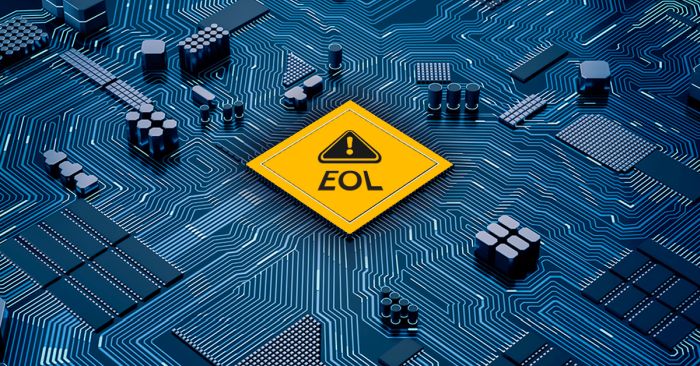
L’obsolescence est inévitable. Le temps passe, la technologie vieillit, mais l’obsolescence n’est pas la fin. Un produit obsolète peut toujours être disponible, un produit obsolète peut toujours être planifié ; un produit obsolète peut faire économiser de l’argent aux entreprises. Le défi exige de la planification et de la préparation, mais faire face au problème permet d’améliorer la situation. Rochester Electronics présente 6 étapes pour gérer l’obsolescence des composants.
Les meilleures méthodes pour planifier et minimiser à la fois les coûts de l’obsolescence.
- La gestion de l’obsolescence commence dès les phases de conception et de définition du produit.
La sélection des composants en cours de développement est un facteur décisif dans les éventuelles reconceptions et requalifications prématurées des produits. Nous avons tous entendu des histoires de produits lancés avec des composants obsolètes. Il s’agit d’une question particulièrement pertinente pour les clients ayant de longs cycles de développement et de qualification. Les nouvelles voitures, les nouveaux avions ou contrôleurs industriels exigent généralement des étapes de conception et de qualification pouvant durer 5 ans. Ajoutons à cela 5 à 7 ans de production et 7 à 10 ans de service après-vente, il n’est pas inhabituel de nécessiter plus de 20 ans d’approvisionnement en composants.
Choisir la bonne technologie de composants et le bon fournisseur peut avoir un impact considérable sur la disponibilité à long terme. Les sources les moins coûteuses peuvent ne pas être le meilleur choix pour un approvisionnement à long terme. Il est difficile d’obtenir des garanties absolues de disponibilité des stocks à long terme, car il peut y avoir des catastrophes naturelles imprévues, des instabilités du marché et des acquisitions de produits, qui ne peuvent pas être prévues des années à l’avance. Par conséquent, un fournisseur fiable doit démontrer un processus de transition éprouvé jusqu’à la fin de vie (EOL) et vers l’approvisionnement autorisé à long terme et la production à long terme. Il est impératif de demander à tout fournisseur quels sont ses engagements en matière de disponibilité à long terme.
Questions clés à considérer :
- Quel est l’état du cycle de vie des composants tout au long de la durée de vie de l’application ?
- Les composants clés de la conception (microcontrôleurs avec logiciel, FPGA ou ASIC) sont-ils entièrement documentés ?
- Les véritables fichiers de conception (VHDL, Spice-Models, Test-Vectors) peuvent-ils être conservés et archivés lors de la phase de conception pour offrir une chance de reconstruction si l’inattendu se produit ?
- La conception contient-elle une propriété intellectuelle exclusive ? Si tel est le cas, la capacité de « porter » une telle conception lorsque les composants sont rendus obsolètes, sera compromise ou soumise à une nouvelle licence et à des redevances.
- Comprendre les coûts totaux de l’obsolescence
Il est important de comprendre et de modéliser les coûts et les risques associés à l’obsolescence. L’obsolescence des composants n’est jamais qu’un problème d’achat à traiter après coup.
Questions clés à considérer :
- Le plan de projet doit-il inclure une actualisation ou une refonte anticipée du produit pendant sa durée de vie ? Si oui, comment sera-t-elle financée ?
- Comment l’entreprise comptabilisera-t-elle le capital bloqué dans l’approvisionnement en composants à long terme ?
- Quel sera l’impact de l’obsolescence des composants sur les engagements de SAV ?
- Quel effet un cycle de vie de produit raccourci aurait-il sur vos clients et utilisateurs finaux ?
- Planification de la gestion de l’obsolescence et des ressources
Si votre équipement se caractérise par de longues phases de qualification, de production ou de durée de vie en service, vous serez confronté à l’obsolescence des composants. Les fabricants qui s’étonnent de l’obsolescence des composants et la considèrent comme un inconvénient peu coûteux à surmonter en paieront le prix sous forme de perturbations, de coûts et de risques.
Les meilleures organisations consacrent des travailleurs multidisciplinaires qualifiés à la gestion de l’obsolescence. La planification préventive par les acheteurs, les ingénieurs en composants, les concepteurs et les responsables de programmes peut réduire ou éliminer les coûts et les risques. Comme le dit l’adage, « le diable est dans les détails » et l’analyse des coûts doit être faite ligne par ligne. L’obsolescence inattendue d’un transistor à 1 cent pourrait potentiellement arrêter un programme dans son élan, tout aussi facilement que l’obsolescence du microcontrôleur principal.
- Identifiez les avis de cessation de commercialisation de produit (PDN) importants qui peuvent affecter votre entreprise et surveillez-les.
La surveillance proactive des cycles de vie des composants est essentielle pour anticiper les problèmes avant qu’ils ne surviennent. D’excellents outils commerciaux sont disponibles pour suivre le cycle de vie, les délais et les changements de spécifications d’un composant. Ces outils fournissent des alertes qui peuvent être déclenchées lorsque des PDN sont émis. Gardez à l’esprit que ces outils utilisent des trackers de marché actuel pour estimer la durée de vie restante des composants.
Il existe des bases de données de gestion génériques permettant aux utilisateurs de charger des structures de nomenclature dans la base de données correspondante, en mettant en évidence tout PDN affectant les produits spécifiés. Chaque fabricant dispose de son propre format de PDN unique. Évaluer et enregistrer manuellement tous les numéros de pièces concernés peut s’avérer extrêmement chronophage. Certains PDN peuvent contenir plus de 500 références.
Il est de plus en plus difficile pour les fabricants de savoir quels PDN affectent leurs produits. L’augmentation des intégrations de systèmes et l’utilisation du traitement intégré signifient que les fournisseurs de second rang contrôlent ces nomenclatures. L’obsolescence des composants mal gérée dans l’un ou l’autre de ces domaines peut toujours déclencher une refonte inutile pour le propriétaire du système global, ainsi que tous les coûts associés.
Questions clés :
- Vos prestataires de second rang partageront-ils leurs nomenclatures ?
- Vos prestataires de second rang ont-ils mis en place des processus de gestion de l’obsolescence adéquats ?
Alors que bon nombre des meilleurs fabricants de composants électroniques (CEM) proposent une gestion proactive du cycle de vie des composants sous forme de service, d’autres sont parfaitement réactifs. Il est important de savoir si un CEM a mis en place un processus de gestion de l’obsolescence adéquat. Les notifications PDN ne sont généralement destinées qu’aux acheteurs directs du composant au cours des 2 dernières années. Une production intermittente ou irrégulière, ou un service après-vente de bas niveau, peuvent ne pas déclencher la notification PDN.
- Last Time Buy (LTB) – Que prévoir ?
La prévision n’est pas une science exacte et, malheureusement, il est probable que les prévisions soient inexactes. Il est difficile d’anticiper les besoins en produits des années à l’avance ou les éventuelles perturbations du marché. S’il est difficile de prévoir la production, il peut être difficile de prévoir avec précision les besoins après-vente. Sous-estimer les besoins comporte un risque d’arrêter prématurément un produit et de perdre des ventes. La surestimation des besoins immobilise des capitaux inutiles en stock, tout en occasionnant des frais de stockage excessifs. De plus, si une refonte est prévue à l’avenir pour limiter le coût du LTB, la conception, la requalification et les coûts d’opportunité liés à l’utilisation de précieuses ressources d’ingénierie doivent tous être pris en compte.
Bien qu’il existe très peu d’options au-delà de la passation d’une commande LTB traditionnelle, travailler avec un fournisseur dont la voie de transition EOL établie offre l’espoir d’un stock et d’une production autorisés continus sans risque. Si la demande augmente, si les reconceptions sont retardées ou si les engagements de service sont prolongés, les partenaires du marché secondaire seront en mesure de répondre aux besoins de l’entreprise. Ces fournisseurs offrent un niveau de sécurité supplémentaire au processus de prévision.
- Achetez auprès de sources homologuées à 100 %
Il existe une idée préconçue selon laquelle une fois que le fabricant d’origine arrête de produire un composant, les sources non autorisées ou du marché gris sont la seule option. L’option sans risque d’un fournisseur après-vente agréé doit toujours être le premier choix.
Les risques de composants contrefaits et de mauvaise qualité provenant de sources non autorisées sont importants pour les rendements de production et le temps moyen entre les taux de défaillance (MTBR) sur le terrain. Des tests de niveau inférieur ou non conformes aux normes par des tiers non autorisés donnent une fausse impression de confiance quant à la possibilité de tester l’authenticité. Cette imitation de test est un visuel, une radiographie ou une mauvaise copie partielle des processus de test du fabricant d’origine. Des tests complets à trois températures sont rarement proposés et le risque que des composants de qualité commerciale soient remarqués en tant que pièces industrielles, automobiles ou militaires est toujours possible.
Les risques liés aux composants non autorisés comprennent :
- Mauvaise manipulation : entraînant des dommages ESD et la destruction de l’équipement. À l’extérieur, il n’existera aucune indication qu’une panne s’est produite.
- Mauvais entreposage : chaleur, froid ou humidité excessifs à n’importe quel moment de sa durée d’entreposage. Cela peut entraîner une corrosion externe du plomb et une mauvaise soudabilité ou une pénétration d’humidité dans le dispositif en plastique et une défaillance catastrophique du dispositif, car il est soumis à des températures de refusion.
- Fausse documentation qui imite la spécification d’origine ou ment sur les tests effectués.
- Composants récupérés, remarqués ou reconditionnés se faisant passer pour un autre produit.
Il existe également des problèmes de qualité documentés liés aux produits chimiques étrangers. Les produits chimiques de nettoyage utilisés pour récupérer, laver et re-marquer les composants usagés, migrent lentement dans les produits, court-circuitant et corrodant les fils de liaison et les tampons. Des tests superficiels ne garantissent pas de trouver ces défauts. Les composants récupérés peuvent non seulement réussir ces tests, mais aussi survivre pendant une période de fonctionnement. Cependant, leurs échecs inévitables détruiront les chiffres MTBR et entraîneront une fiabilité réduite et des réputations endommagées.
Les fabricants de composants d’origine (OCM) ne fournissent aucune garantie pour les produits achetés via des canaux non autorisés. Beaucoup interdisent explicitement la vente de composants à des sources non autorisées.
Les sources autorisées, telles que Rochester Electronics, offrent un approvisionnement sans risque et sont la seule option vraiment sûre pour maintenir les lignes de production des clients opérationnelles en cas de pénurie, d’allocation et d’obsolescence.
Les distributeurs entièrement autorisés, comme Rochester Electronics, sont conformes à la norme aérospatiale SAE, AS6496. En termes simples, ils sont autorisés par le fabricant de composants d’origine à fournir des produits traçables et garantis sans qu’aucun test de qualité ou de fiabilité ne soit requis, puisque les pièces proviennent du fabricant de composants d’origine. Rochester est homologué à 100 % par plus de 70 grands fabricants de semi-conducteurs.
Les fournisseurs qui ne sont pas pleinement autorisés peuvent se commercialiser comme étant conformes à la norme AS6171/4. Cela indique qu’ils respectent des inspections et des procédures de test normalisées, mais peuvent avoir des exigences minimales de formation et de certification pour détecter les composants suspects ou contrefaits. Si le test AS6171 est en cours, cela signifie que le produit n’est pas testé selon le programme de test OCM. Les programmes de test OCM testent de manière significative au-delà des paramètres de la fiche technique et sont destinés à filtrer le produit pour qu’il ne disparaisse pas, même lorsque des millions d’unités sont vendues. Le test AS6171 n’est pas équivalent au test OCM. Bien qu’il soit toujours mieux que l’absence totale de conformité, si le test AS6171/* est proposé isolément, cela indique potentiellement que les pièces ne proviennent pas directement de l’OCM, mais qu’elles ont seulement réussi le test AS6171. Cela réduit davantage que cela n’élimine le risque.
Plus de 10 milliards de composants en stock de Rochester sont classés comme EOL par le fabricant d’origine, à partir duquel le produit est directement fourni. Rochester est bien placé pour offrir une source d’approvisionnement continue pour les applications lorsque le cycle de vie du produit s’étend au-delà de la disponibilité active d’un composant. Les offres directes d’usine de Rochester éliminent le besoin d’une reconception, d’une requalification, d’une recertification coûteuses et évitent le risque de s’approvisionner en produits difficiles à trouver sur le marché libre. Les composants sont homologués à 100 %, traçables et garantis directement par les OCM. En conséquence, Rochester peut offrir les garanties des composants d’origine.
En tant que fabricant de semi-conducteurs sous licence, Rochester propose des solutions continues utilisant des informations et des technologies transférées directement à Rochester depuis l’OCM. Rochester utilise les processus de matrice et de fabrication du fabricant d’origine, correspondant aux conceptions, aux solutions d’assemblage et aux protocoles de test originaux. Tous les produits en résultant sont certifiés à 100 %, sous licence, garantis et vendus avec une homologation complète sous la référence du fabricant d’origine.
Les solutions de fabrication sous licence de Rochester sont le code de date actuel, garanti conforme aux performances de la fiche technique d’origine, et notre équipe est prête à aider les clients à naviguer à travers des exigences réglementaires strictes. Rochester a fabriqué plus de 20 000 types de composants. Avec plus de 12 milliards de dies en stock, Rochester a la capacité de fabriquer plus de 70 000 types de composants.
Pour mieux répondre au besoin continu du client de prolonger la durée de vie des produits semi-conducteurs, Rochester continue d’investir dans des solutions de conception, garantissant que votre logiciel système n’a pas besoin de changer, tout en créant simultanément des solutions matérielles instantanées qui minimisent les nouvelles dépenses de qualification. Rochester se spécialise dans le portage autorisé de produits issus de processus de fabrication originaux, mais propose également des remplacements de forme, d’ajustement et de fonction. Quelle que soit la solution de conception de Rochester, aucun errata n’est introduit et aucune modification du logiciel système n’est nécessaire.
Anticipez et planifiez l’inattendu. Il est aujourd’hui plus vital que jamais d’avoir des partenaires capables d’accompagner les entreprises lors d’arrêts de composants imprévus ou non planifiés, sans aucun risque lorsqu’ils se produisent.
CE PUBLI-RÉDACTIONNEL A ÉTÉ RÉDIGÉ PAR ROCHESTER ELECTRONICS